
Honda, a Japanese car manufacturer has demonstrated outstanding results in their recent project intended to reduce the weight of the crankshaft and increase its fuel efficiency. In order to carry out such a redesign in an effective and timely-fashioned manner, the company collaborated with Autodesk and applied its software solutions, as well as various 3D-printing technologies.
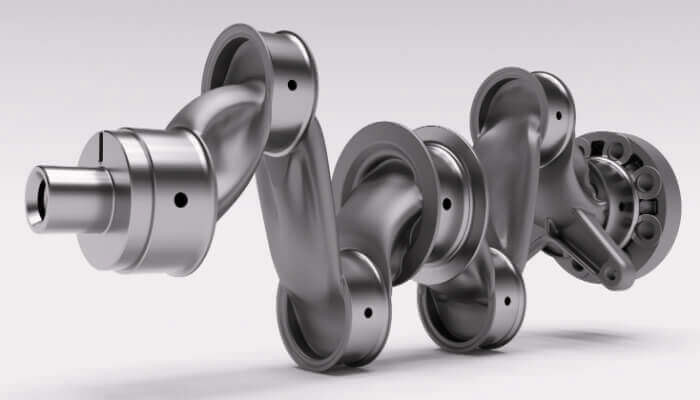
The above-mentioned project is the first of many others dedicated to one specific and global task. Honda aims to redesign various vehicle parts such as gears, frames, and fasteners in order to make them more lightweight, fuel-efficient and eco-safe. The company is already familiar with 3D-printing technologies and applied it in previous projects. In 2016, for example, Honda presented a prototype of a new electric delivery vehicle with a customizable 3D-printed body. The main idea is that additive manufacturing can help reshape courier vehicles in a manner that will further highlight and advertise the offered product.
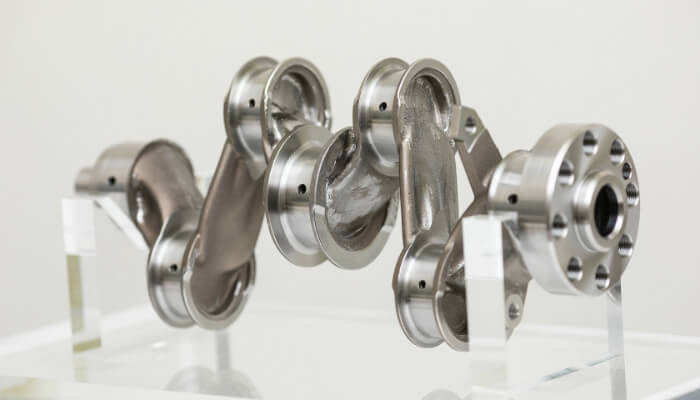
But the engines have to be modernized too, and the company’s new project reviews the possibilities of crankshaft optimization. The research was conducted in close collaboration with Autodesk, which invited some specialists of Honda’s R&D department to attend training courses in London and learn about working with such software solutions as Fusion 360 and Nettfabb in the most efficient way. After that, the specialists were relocated to Birmingham in order to visit the Autodesk Technology Center with a number of industrial 3D-printers. The possibilities provided by generative design were in the middle of attention: the employees of Autodesk presented the first version of the product in accordance with project requirements, and then the teams joined efforts in order to modify and release the final version of the crankshaft.
Hirosumi Todaka, a mechanical and fluid machinery modeling engineer of Honda explains: “Crankshafts need to satisfy multiple functional criteria. For example, its shape must be able to withstand combustion pressures, and the rotational balance must be maintained. These factors have dictated the crankshaft’s form to this day. Over the long history of engine development, the crankshaft design had become a foregone conclusion. Despite this, we set the challenging goal of designing a crankshaft to be 30% lighter than current models.”
In the end, the project outcome was a great success, since the team designed a crankshaft 50% lighter than the current model. As Todaka stated, some of the configuration provided by Fusion 360 generative algorithms were so unique that he couldn’t have come up with such by himself. The crankshaft was integrated into an assembled prototype and has successfully passed all the bench tests. The data received during the project has been transferred to Autodesk in order to further upgrade and modernize already existing algorithms of generative design.